Yuelongshan Shengxing Temple in Takaoka City, Toyama Prefecture, Japan was built in 1584 and was designated as an important national cultural heritage by Japanese officials.This national treasure -level ancient temple is well -maintained and perfect. It is both antique and not losing the sense of the times. All because of a group of skilled temple maintenance craftsmen, it is constantly repaired.In July 1998, Shengxing Temple launched a repair project. The semi -solution -type project has lasted for more than 20 years. There is still a small project that has not been finished, and the cumulative cost is about 7 billion yen (about S $ 69 million).
The 40 -year -old History of Zhou Mu is a carpenter that is a rare work for renovation for ancient temples and national cultural heritage.Since Shengxing Temple launched a repair project, he has entered the industry to study the architecture with his master, and now he has been a beam in the ancient building restoration craftsman.
Zhoumu told Lianhe Zaobao that woodworking is a representative technology of traditional Japanese architecture. The biggest feature is that it does not use nails in the structure, but is assembled from unevenly cut wood.Therefore, the processing process should be particularly careful and choose wood based on experience.
He said: "The repair engineering technology we use comes from the Edo period (1600 to 1868). The hardest step of the most difficult maintenance of ancient cultural relics is to connect the new wood to the old wood, which is the same as creating one on the open space.The new building is completely two different worlds. The most challenging is the demolition project, and you must be careful to observe the essence of the old building. These knowledge can not be learned in textbooks.Have a serious research spirit. "
"Gong Gonggong" must have knowledge and history knowledge
The Japanese call the construction industry workers "big workers", and craftsmen who specialize in repairing shrines and temples like Zhoumu are also called "Gong Grand Workers".Although Japanese officials have not issued a diploma of palace engineering so far, these craftsmen's knowledge in the construction industry is broader than ordinary craftsmen, because they must have the accumulation of humanities and history.When renovating and repairing shrines or temples, they must deeply understand the characteristics of various denominations in order to design details for temples and shrines.
The protection of traditional cultural heritage in Japan can be said to be in front of other countries.Japan conducted a large -scale ancient building census in the Meiji era, and promulgated the ancient club temple preservation law in 1897 to strengthen the protection of ancient temples.However, in modern Japan, most of the young people went to the city to make a living. Because no one took over, the maintenance industry appeared faults.
Takada Kehong, a director of the cultural preservation and use of Shengxing Temple, said that there are more than 70,000 temples in Japan, more shrines, and more than 81,000, but only about 100 people in Japan can perform repair work.
Takada said: "Lagsmith is a physical worker. The older the age, the limited the work that can be assumed. As the Japanese population ages, this specialized work has been successively succeeded. Although the newly -built temples and shrines in Japan have decreased, they have decreased, but they have decreased, but they have decreased, but they have decreased, but they have decreased, but they have decreased, but they have decreased.The existing buildings are aging year by year. If the inheritance and repair technology and cultivation successors are not stepped down, the protection of cultural heritage will face a great crisis. "
Japan's officially established Population Countermeasure Committee's future population map released by Japan in 2014 predicts that in 2054, 896 cities and villages in Japan will disappear due to the sparse population.
Japanese Shrine and Temple are no exception.The above -mentioned population map estimates that 35.5%of monastery and shrines will disappear from historical torrents.
Ishikawa County Vocational University Training Professional Craftsman
Ishikawa Prefecture, which is adjacent to Toyama Prefecture, founded the "Kanazawa Vocational School" in 1996. It is the first school in Japan to make craftsmen study.The school offers a three -year course for artisans across Japan for study.The school only collects 50 students each year, and the average age of students is about 50 years old. There are woodrs, stone artisans, tiles and tatami craftsmen.
The materials for the study of craftsmanship are all dilapidated pillars and doors and windows in ancient Japanese buildings.They carefully studied for every old structure, and discussed with craftsmen from different places.
The school understands that craftsmen are not good at text and computer records, so they arranged civil servants in the civil engineering department and architectural designers in the company to regularly go to the school to enter the computer archive.
The 59 -year -old construction worker Ogawa Kangyan goes to school every week and is now a junior.He said gratefully: "For decades in the construction industry, I never thought that I can go to college at this age, and I explore the traditional Japanese architectural technology. I feel that I have become a researcher from a craftsman. Construction.The technology is changing with each other. I must have applied it. Not only should I assist in repairing Japanese cultural relics, but also to pass the knowledge I understand to the next generation. "
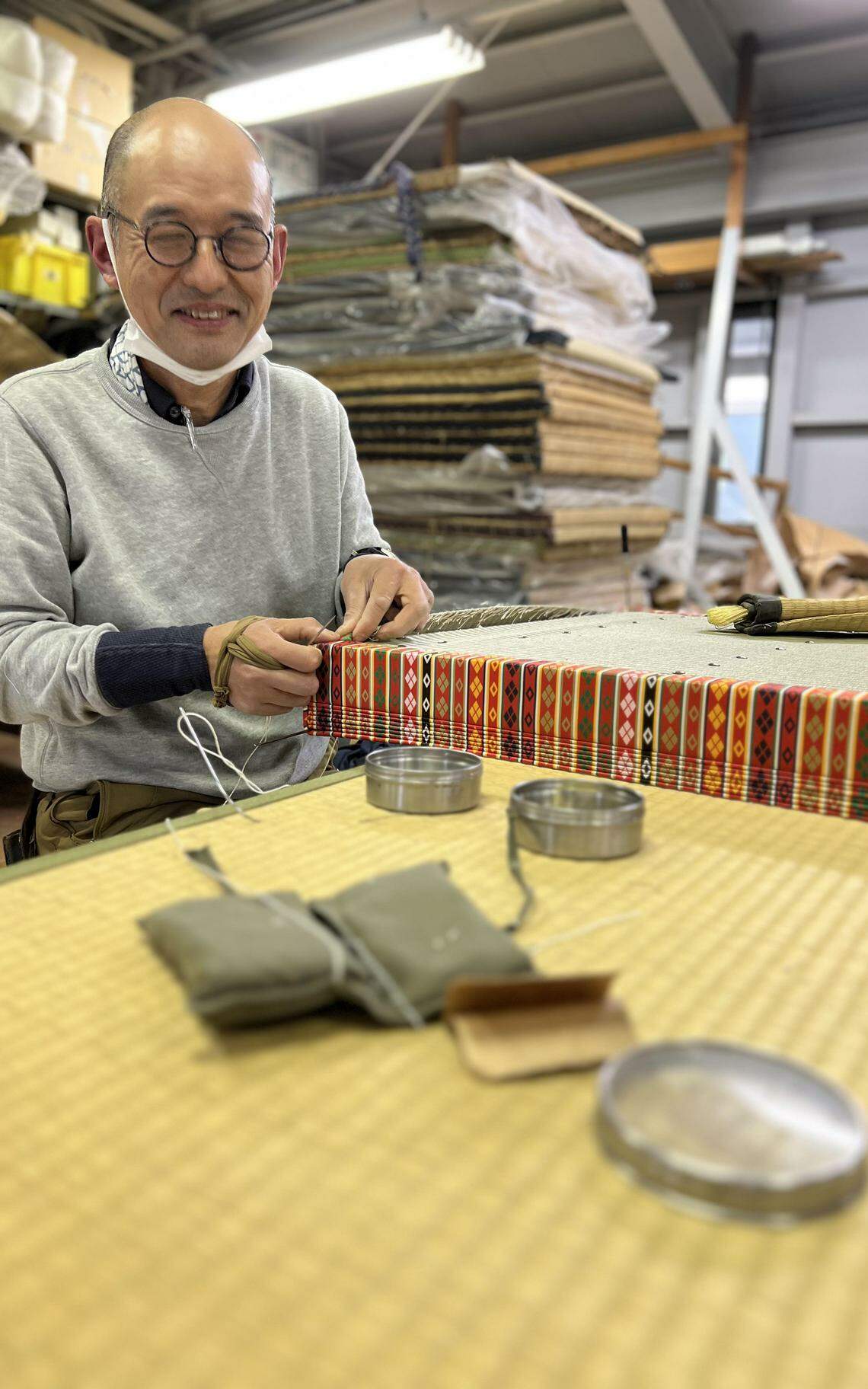
The 28 -year -old Katsuhara Xuanta is a tatami craftsman from Osaka. He inherits his father's tatami workshop and is the sixth generation heir of the family business.
He said: "I lack awareness of the traditional tatami. Now, many tatami is already a finished product, and I am not a craftsman in my usual work.Self -improvement. "
A temple in the classroom where I was located used for more than 90 years of tatami. The surface was scattered, but the light hearts inside were still white.
A instructor said: "This is a traditional tatami with real materials. As long as it is repaired, you can use it for 50 years. This university is not only taught by craftsmanship. We hope to use ancient cultural relics to let students know about it.Go to the essence of handicrafts left by generations of craftsmen. "
There are only 15 gold foil artisans left in Kim Ze
The Japanese government not only pays attention to the protection of ancient cultural relics, but also attaches great importance to cultural heritage such as traditional craftsmanship and art.The golden foil produced by the Kimsuawa District of Ishikawa Prefecture is glittering and dazzling. It is the traditional craft product with the highest gold content in Japanese handicrafts.
The traditional skills, technology and knowledge related to the protection and inheritance of Japanese wooden buildings, which was accepted by the United Nations Education, Science and Cultural Organization as an intangible cultural heritage in 2020."Technology.
Kawaka Kawasawa, director of the Institute of Golden Foil Technology, told reporters that the production technology of gold foil has been inherited for more than 400 years. The craftsmanship and the Japanese and paper used to make gold foil determine the quality of the gold foil.Create gold foil must be used with paper, with high -quality harmonious paper to knock thick gold into a shiny ultra -thin gold foil.Although gold foil manufacturing technology originated from Kyoto, 99%of gold foil in Japan is produced in Golden.Gold foil is used in buildings such as temples and Buddha statues, and is also a classic material for noble arts and crafts.
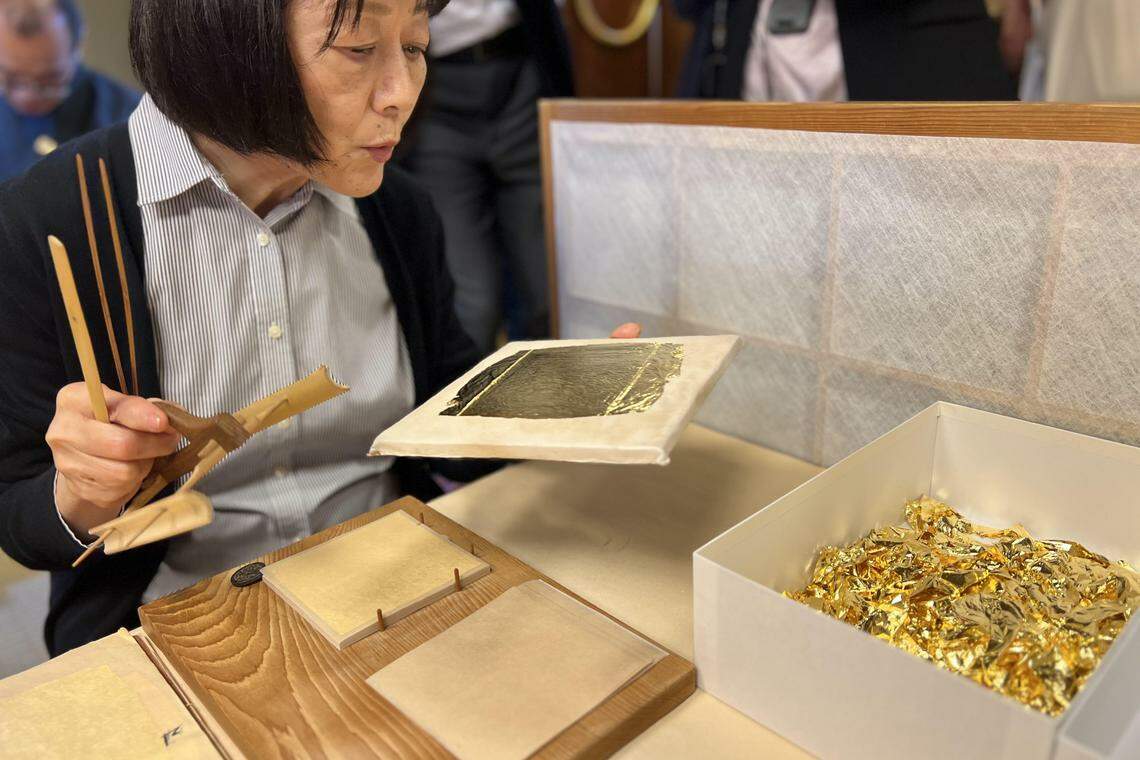
However, when talking about the future of this craft, Kawakami Kawakami was sorrowful.According to him, the environment of the production of gold foil has changed a lot.In the past, the gold foil market expanded rapidly in the era of high economic growth, mainly used for the decoration of the Buddhist altarEssenceIn recent years, this demand has continued to shrink because the repair of temple shrines and cultural buildings with high demand has stagnated.
The crown disease epidemic also worsen this industry, because tourists' demand for gold foil products has been reduced.Before the epidemic, the output of gold foil in Ishikawa County was about 2.57 billion yen, which reduced to 1.45 billion yen by 2021.The Russian and Ukraine War led to soaring gold prices, which also greatly increased the cost of this industry.
The most severe problem is that there are no successors.Half a century ago, there were about 200 milling artisans producing gold foil. Today, this number has been reduced to one -tenth of the original.There are only 15 people in Ishikawa County, and the average age is over 70 years old.
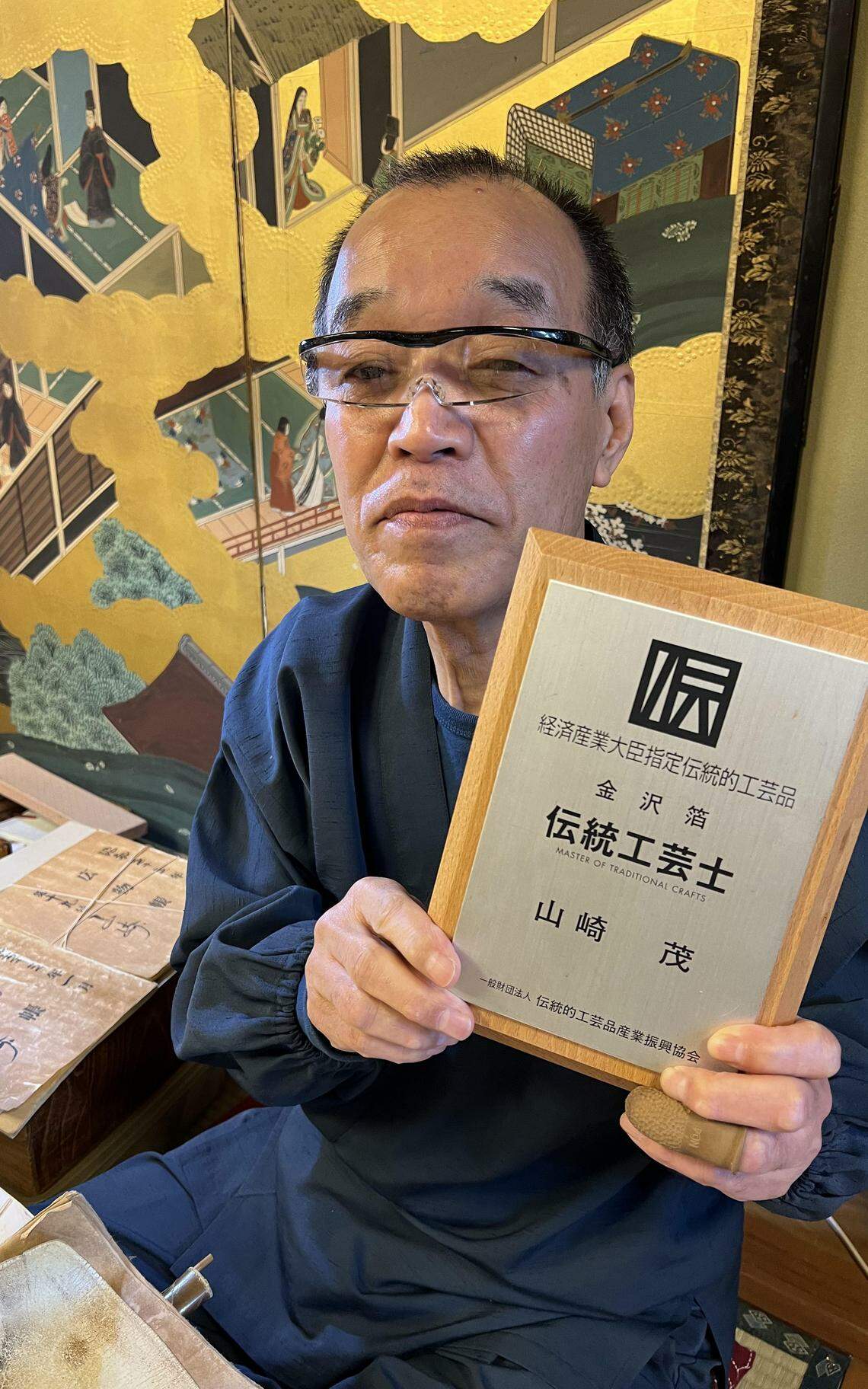
As one of the only 15 people, the 75 -year -old gold foil grinding artisan Yamazaki Yamazaki has been inherited his father's mantle for 45 years. The reason why he could not retreat was that his son was unwilling to be a successor.
He told Lianhe Morning Post: "In this industry, you have to go to a teacher for 10 years. Naturally, it is no easier than going to the company. I am also willing to pass the crafts to outsiders, but I have never asked.
At present, Yamazaki Mao and his wife work in a store of a gold foil product agent every day, and regularly host an experiential gold foil production class.He hopes that through such arrangements, people can observe the charm of gold foil manufacturing at close range and attract interested people to enter the industry.
Foreign -funded participation in the cultivation of gold foil craftsmen
In Japan, local governments have policies aimed at protecting and inheriting traditional craftsmanship, such as institutions that support traditional craftsmanship, and systems that assist handicraft promotions in various places. There are also financial budgets that support the cultivation of young craftsmanship.
Gold foil production technology in the Kim Ze area entered the ranks of the world's intangible cultural heritage, which also attracted the attention of foreign capital.
The artisan training plan of the American jewelry brand Tifanny Co., to assist the Golden Ze Traditional Gold Foil Technology Preservation Association to set up a craftsman training program called "Golden Zeyuan Moon Foil".This project recruits four students 20 to 50, and is expected to become the heir to the production skills of gold foil in the future.
As the epidemic of crown disease eases, overseas tourists have increased, the gold foil business district in Kanazawa has recently become lively.In addition, there are many gold foil products for exports.
Kanazawa ’s Takayami Foil Foil Company said:" Promoting the tourism industry is one of the ways to continue the handicraft. In the past, Kinosawa could become the center of the gold foil manufacturing industry because there were more adjacent Kyoto Ancient temples, But gold foil can also be used on many daily necessities, even cosmetics and food. In order to continue traditional culture and technology, we must not only diverse the use of gold foil, but also strive for internationalization. "
Toyama Hymeric Industrial Arts and Research Become a Glass Talent Base in Japan
Toyama City, Toyama Prefecture is the capital of glass in Japan. It not only produces glass products, but also develops glass art.The local glass industry is developed because of the drug industry with a history of more than 300 years, and the early oral drugs in Japan were installed in the glass bottle.
In 1985, the Toyama Municipal Government launched a project called "Glass Town". The biggest purpose was not to promote glass crafts, but to make the city the core base of "cultivating glass handicraft talents".
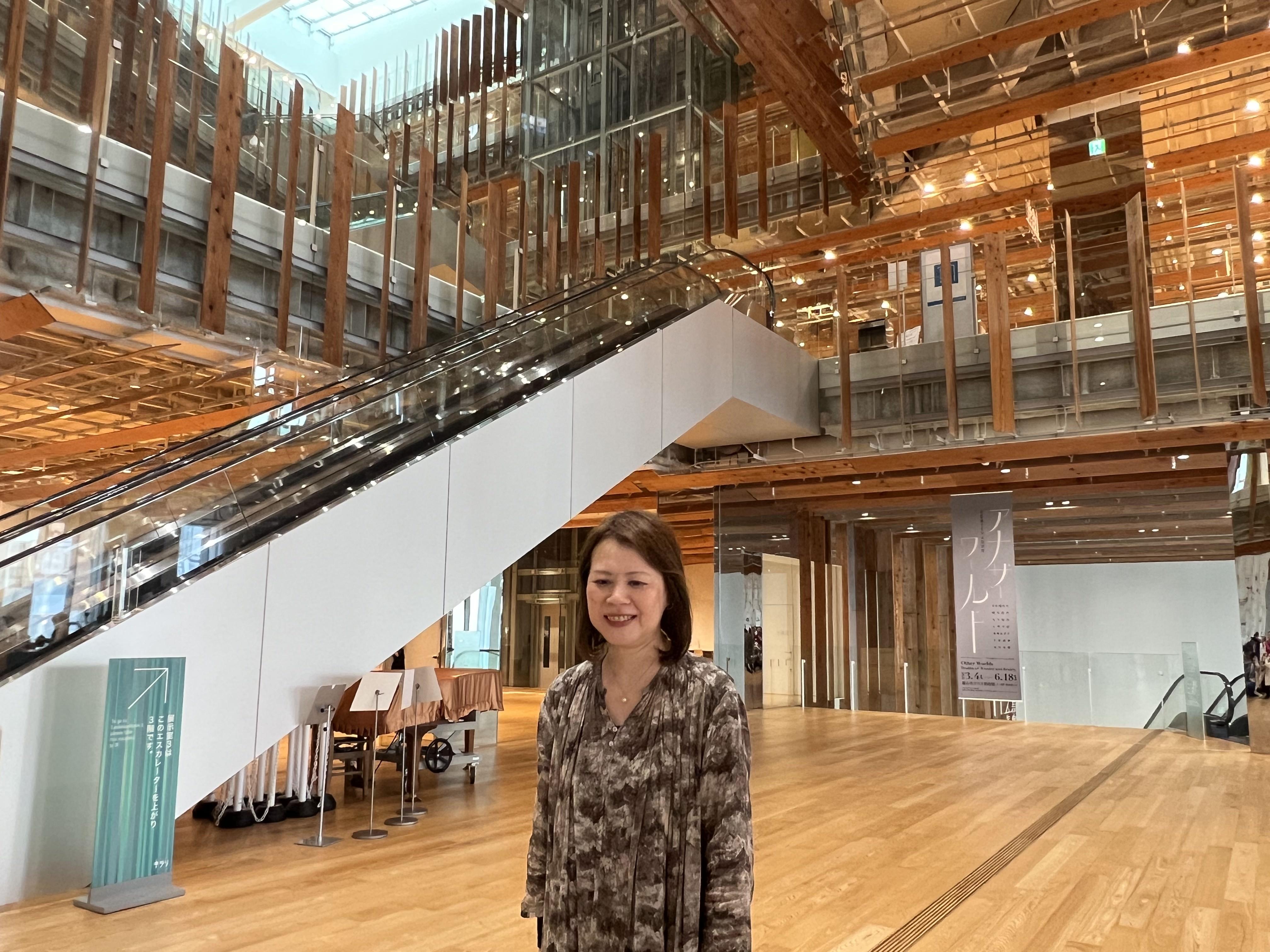
The Toyama Municipal Government has created the only "Glass Style Style Research Institute" in Japan with the qualifications to cultivate glass artists and set up a workshop for glass artists.There are more than 400 glass artworks from all over the world.
In the interview, the director of the Museum of Art Museum said: "The Glass Style Style Research Institute, the workshop and the art museum are interacting. This combination allows the glass to not only have appreciation value in Toyama, but also have research and development.Help and develop crafts and training artists. In addition, this form also makes it easier for us to connect with glass experts, merchants and artists from all over the world. "
The Toyama Glass Style Institute is the only public glass college in Japan. In addition to the people who are interested in making glass in China, there are also overseas glass experts and international students.
Promoting environmental protection and reuse is a subject of active thinking in the Japanese art world.Jaroslov Sara, an associate professor from the Czech Republic and coached at the Toyama Glass Style Research Institute, said that although the Japanese population is shrinking, the talents of the art world are also very prominent about the reuse technology of abandoned glass.
According to local statistics from Toyama, glass of glass and other facilities accumulated as mountains.The Toyama Glass Style Research Institute collected them and reorganized.Researchers removed the impurities, and after melting, it was found that the glass showed a mysterious blue.Because the glass -saving method with a power saving method of 40 degrees Celsius is far below the glass melting point of less than 1,400 degrees Celsius to 1600 degrees Celsius, the local glass art is also at the forefront of environmental protection.
A famous Japanese glass artist Akata Miya, known as the "Magic Magician", said in an interview that art can cooperate with technological growth to make the artist's creation show a new style.
"The artist is also a craftsman and a researcher. The glass lace materials used by my works are made of myself, and each work must be made after many experiments."
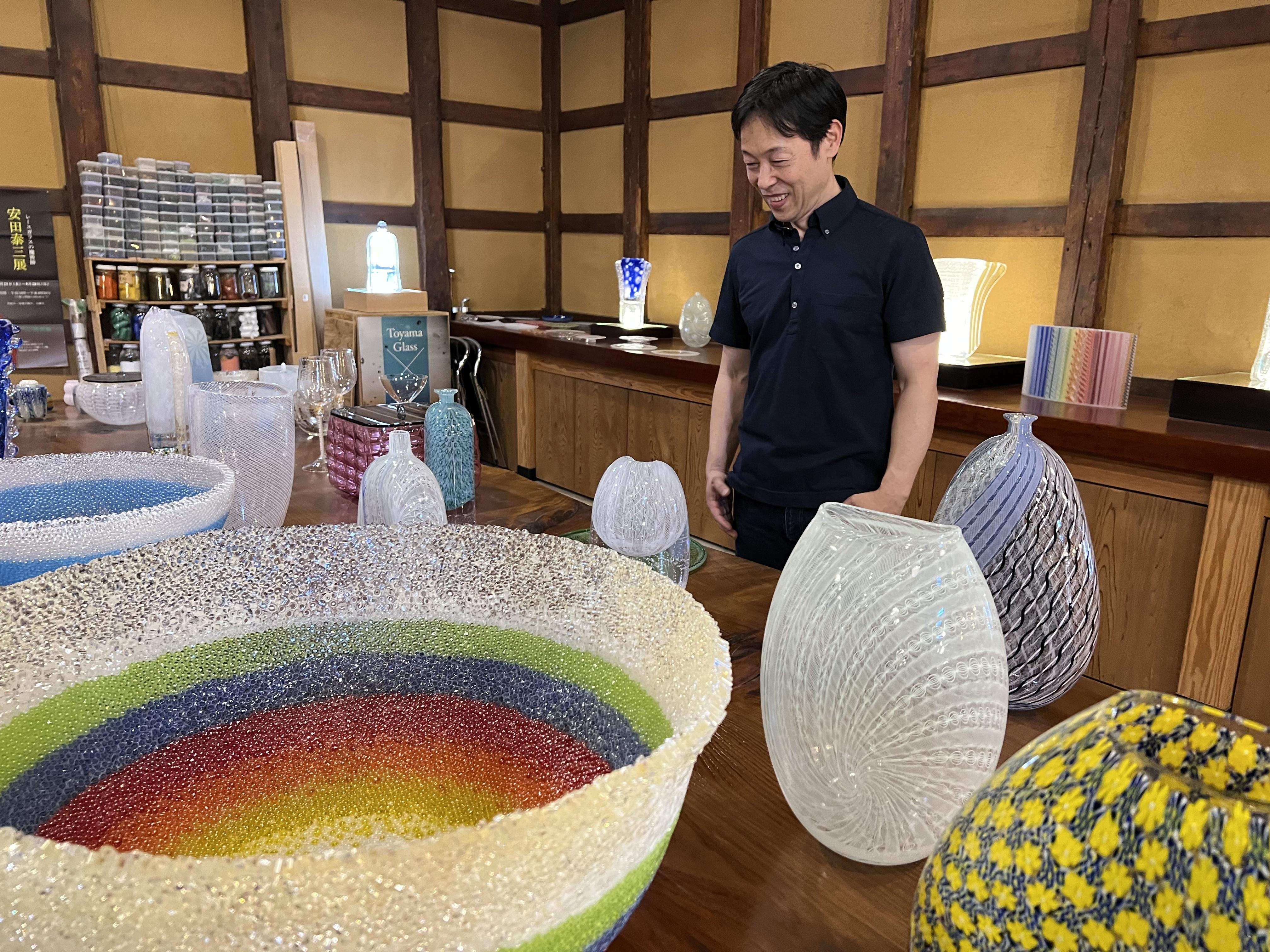
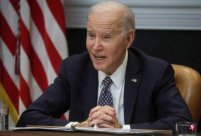
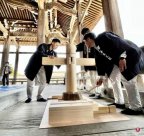
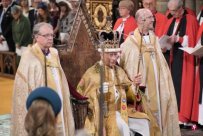
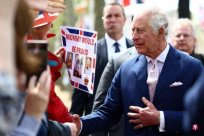